The Science Behind Porosity: A Comprehensive Guide for Welders and Fabricators
Recognizing the elaborate devices behind porosity in welding is essential for welders and fabricators pursuing remarkable workmanship. As metalworkers delve right into the depths of this phenomenon, they discover a world regulated by numerous elements that affect the formation of these tiny voids within welds. From the structure of the base materials to the intricacies of the welding procedure itself, a plethora of variables conspire to either worsen or minimize the existence of porosity. In this extensive overview, we will unwind the scientific research behind porosity, exploring its effects on weld high quality and introduction progressed techniques for its control. Join us on this trip with the microcosm of welding imperfections, where precision satisfies understanding in the quest of flawless welds.
Recognizing Porosity in Welding
FIRST SENTENCE:
Assessment of porosity in welding exposes vital insights into the honesty and top quality of the weld joint. Porosity, characterized by the existence of tooth cavities or gaps within the weld steel, is a typical worry in welding procedures. These voids, otherwise appropriately addressed, can compromise the structural stability and mechanical residential properties of the weld, causing possible failings in the completed item.
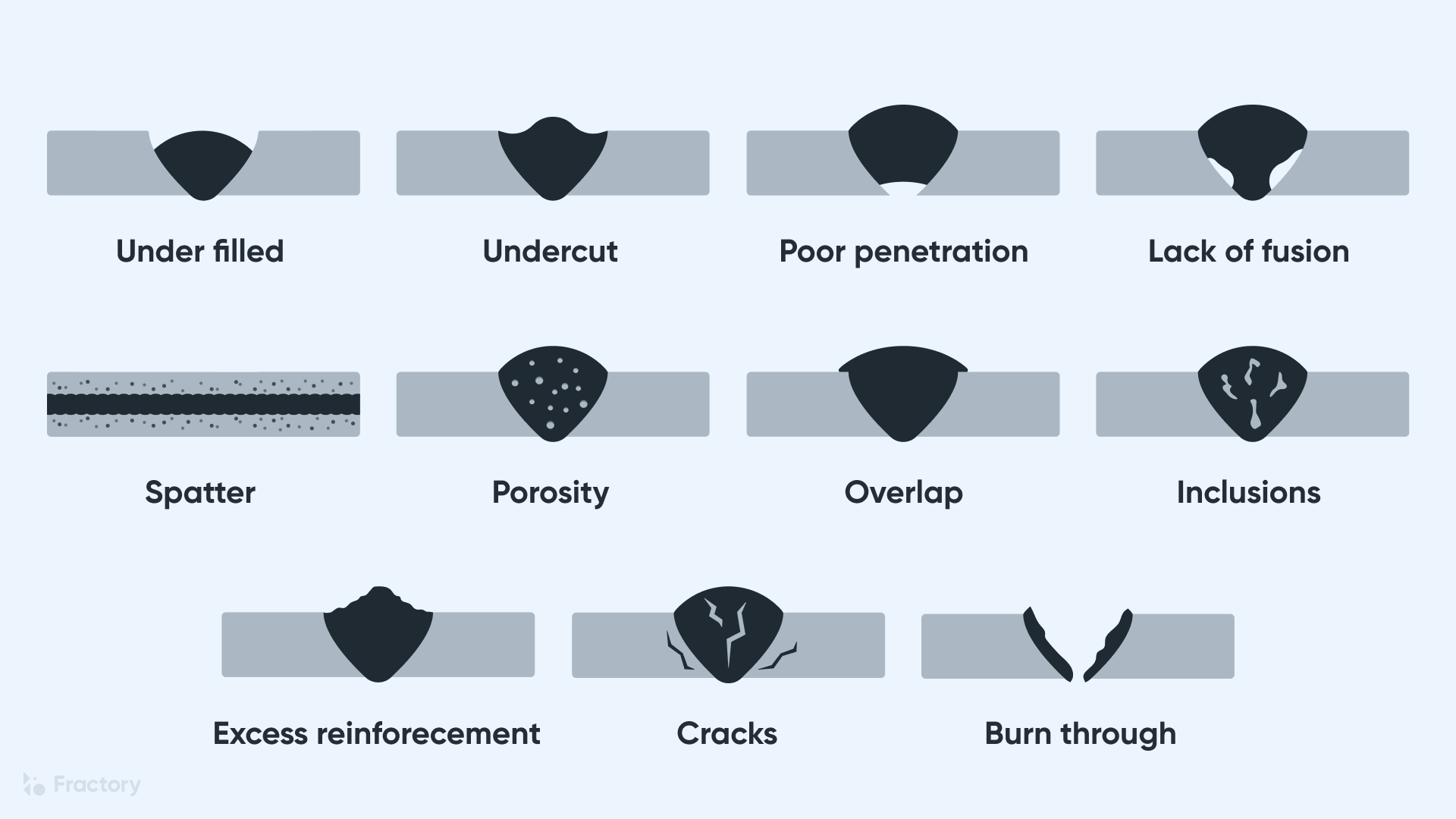
To identify and measure porosity, non-destructive testing methods such as ultrasonic testing or X-ray examination are commonly utilized. These techniques permit the identification of interior problems without compromising the integrity of the weld. By assessing the dimension, shape, and circulation of porosity within a weld, welders can make educated decisions to boost their welding processes and achieve sounder weld joints.

Factors Affecting Porosity Formation
The occurrence of porosity in welding is influenced by a myriad of aspects, varying from gas shielding efficiency to the details of welding parameter settings. Welding specifications, consisting of voltage, current, travel speed, and electrode type, likewise influence porosity development. The welding strategy employed, such as gas metal arc welding (GMAW) or protected steel arc welding (SMAW), can affect porosity development due to variants in warmth distribution and gas protection - What is Porosity.
Impacts of Porosity on Weld Top Quality
Porosity development considerably jeopardizes the architectural honesty and mechanical properties of bonded joints. When porosity is existing in a weld, it develops gaps or tooth cavities within the product, reducing the total toughness of the joint. These gaps function as tension focus points, making the weld extra susceptible to splitting and best site failing under load. The visibility of porosity likewise deteriorates the weld's resistance to special info corrosion, as the entraped air or gases within the voids can react with the surrounding atmosphere, bring about destruction with time. Additionally, porosity can hinder the weld's ability to stand up to pressure or effect, additional jeopardizing the overall high quality and reliability of the welded framework. In vital applications such as aerospace, auto, or structural building and constructions, where safety and longevity are extremely important, the harmful impacts of porosity on weld top quality can have serious consequences, highlighting the relevance of reducing porosity with correct welding methods and procedures.
Strategies to Decrease Porosity
In addition, using the suitable welding specifications, such as the proper voltage, existing, and travel speed, is important in protecting against porosity. Keeping a consistent arc length and angle during welding also assists minimize the probability of porosity.

Making use of the ideal welding strategy, such as back-stepping or utilizing a weaving motion, can additionally assist distribute heat equally and minimize the chances of porosity formation. By applying these methods, welders can efficiently reduce porosity and create top quality bonded joints.

Advanced Solutions for Porosity Control
Implementing cutting-edge modern technologies and innovative approaches plays a critical role in accomplishing exceptional control over porosity in welding processes. Furthermore, employing sophisticated welding techniques such as pulsed MIG welding or customized atmosphere welding can likewise help alleviate porosity issues.
An additional advanced option involves using advanced welding devices. Making use of devices with integrated features like waveform control and innovative power sources can improve weld top quality and reduce porosity dangers. In addition, the implementation of automated welding systems with exact control over criteria can significantly lessen porosity issues.
Moreover, including advanced tracking and examination modern technologies such as real-time X-ray imaging or automated ultrasonic testing can aid in spotting porosity early in the welding procedure, enabling prompt corrective actions. Overall, integrating these innovative solutions can greatly enhance porosity control and improve the general top quality of bonded elements.
Verdict
In find this verdict, comprehending the science behind porosity in welding is essential for welders and producers to produce high-grade welds - What is Porosity. Advanced options for porosity control can additionally boost the welding procedure and make certain a strong and trusted weld.